Sistemas Flexibles de Manufactura.
En un mundo cada vez más interconectado, se hace más frecuente la discusión sobre la necesidad de implementar Sistemas de Recursos Empresariales (ERP por las siglas en inglés de Enterprise Resource Planning), pues se parte de la premisa que dichos sistemas ofrecen la solución ideal para la comunicación de los diferentes procesos llevados a cabos por las personas y departamentos responsables, en tiempo real y a menor costo.
Con el fin de facilitar la comprensión de este debate, este artículo presentará un resumen de lo que es un ERP, sus antecedentes y su fututo.
Una mirada al pasado: MRP y MRP II
Antes de la existencia de herramientas computacionales y en el contexto de las guerras mundiales, las organizaciones, en especial la industria militar, desarrollaron metodologías para gestionar la cadena de abastecimiento y administrar los recursos (humanos, técnicos, equipo). Es así que para la gestión de inventarios, lista de componentes de los artículos y sus subcomponentes se desarrolló la metodología de Planificación de Recursos de Materiales (MRP), metodología que al día de hoy goza de gran popularidad dado que permite proyectar las requisiciones de materiales en función de las demandas de la producción de la planta.
Al poco tiempo, la necesidad de diseñar en forma más expedita y eficiente los planes agregados de producción de acuerdo a los planes de venta (en el caso de las ventas por pedido) o de las estimaciones de inventario de producto terminado (para la producción con base a stock de producto
final) por parte de las grandes plantas de manufactura, llevó al desarrollo de la metodología de Planificación de Recursos de Manufactura o MRP II por sus siglas en inglés, permitiendo planificar la producción desde la orden de compra de la materia prima hasta su puesta en la bodega de producto terminado.
El advenimiento de la era de la información y la posibilidad de almacenar mayores niveles de datos que permitieron la creación de herramientas computacionales para el MRP y el MRP II, dio lugar a la ya evidente necesidad de integrar procesos administrativos y logísticos que afectan directamente a la manufactura: procesos contables, gestión de compras, pago de nómina y otros, que finalmente dio origen a finales de los años 70 del primer ERP de la historia desarrollado por la empresa alemana SAP.
Arquitectura básica de un ERP
En su versión más simple, un ERP consta de los siguientes grupos o familias de módulos:
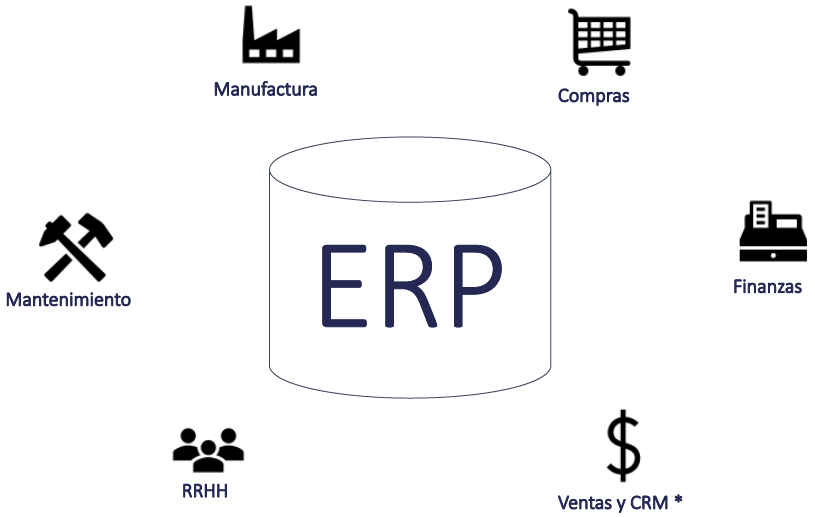
En un ERP, cada uno de estos módulos o familias contiene una o varias aplicaciones que interactúan con el resto. Así por ejemplo, un centro de costo definido en un módulo contable será el que determine un centro de actividad de un submódulo de manufactura MRP II, un activo fijo sea el que se designe la parametrización de una máquina, el costeo de la mano de obra por producto es definida por el sistema de nómina o el sistema de compras el que procesa el ingreso de material en el MRP.
Al estar todos los sistemas administrativos y de manufactura integrados en un único sistema, se presentan ventajas comparativas, como el hecho de ser en principio modulables (se puede prescindir de algunos componentes), parametrizable en función de los procesos específicos de la manufactura y
escalable (permiten crear nuevas familias de productos o servicios).
Estas ventajas presuponen la punta de lanza de la Revolución Industrial 4.0, donde la inmediatez de los datos por información refuerza la tesis de unificar los esfuerzos computacionales y tecnológicos por sistemas de manufactura soportados por un ERP.
El diablo está en los detalles
Los sistemas ERP son antecedidos por las metodologías MRP y MRP II que posteriormente fueron llevadas al software. Pero, pensemos brevemente en una manufactura de derivados del petróleo o derivados de la leche, donde la programación de la producción no se basa en las reglas del MRP ni del MRP II, y por tanto no existe una lista de materias primas, sino una sola materia prima donde se obtienen todos los productos finales ¿cuál sería el valor agregado de una solución ERP que “ad portas” no permite controlar la producción de la principal materia prima como lo podría ser un barril de petróleo o la leche líquida? Este escenario plantea el reto de buscar soluciones intermedias, ya sea con diseño de software secundario, creación de actividades complementarias o una mezcla de ambas, contradiciendo las bondades preliminares de un ERP.
Así mismo, pensemos en una industria ya establecida que cuenta con software especializado para la gestión de la mayoría de sus procesos administrativos, como pudiera ser la industria financiera o las
instituciones educativas ¿vale la pena prescindir de ese software especializado por una solución ERP, donde sus módulos no necesariamente serán especializados como los ya instalados? Esto plantea analizar las variables de escalabilidad, infraestructura y soporte técnico requerido de una solución ERP versus los sistemas legacy actuales.
Por último, pensemos en una planta de manufactura cuyo departamento de programación de la producción cuenta con colaboradores cuya única función es alimentar el ERP con los registros de las hojas de ruta de las órdenes de producción ¿tiene sentido esta actividad en plena revolución industrial 4.0, donde se cuenta con sensores y actuadores en las mismas máquinas, o en su defecto aplicaciones móviles?
Estos escenarios plantean el reto de conocer las fortalezas y debilidades de cada una de las marcas de ERP en el mercado, conocer su “corazón computacional” (proceso funcional básico de interacción intermodular), interconectividad con dispositivos móviles o con sensores al equipo de operación.
Esto sumado a la la experiencia del equipo de negocio y la del equipo de TI son fundamentales para el equilibrio entre una solución basada en ERP versus soluciones no basada en ERP, sea ésta con software legacy o procesos manuales o híbridas entre soluciones ERP y soluciones legacy.
El futuro de los ERPs
El avance de los sistemas computacionales ha permitido la adopción de estrategias de automatización de procesos (RPA por sus siglas en inglés), la ampliación de las posibilidades de los sistemas CRM (Costumer Relationship Management) y el incremento en procesamiento de volúmenes de información de los sistemas de Business Intelligence (BI). Varias marcas de ERP están adoptando estas tecnologías y las apropian como parte de sus sistemas, lo cual sin lugar a duda, darán solución final o cuando menos mitigarán varios de los retos que enfrentan las organizaciones cuando adoptan estas tecnologías. Allí lo importante será valorar la implementación de un sistema ERP (o partes de él) que mejor atienda los retos actuales en las industrias y que responda mejor al futuro de sus necesidades de negocio.
En los casos de organizaciones que por la naturaleza de sus procesos o por el desarrollo orgánico de sus sistemas internas (con múltiples sistemas coexistiendo), con híbridos de algunos componentes de un ERP, sistemas legacy y procesos manuales, el reto consiste en la armonización de los datos en función de los procesos medulares y proporcionar información en tiempo real, que aunque pudiera significar un incremento considerable en la arquitectura de TI, la adopción de sistemas de Business Intelligence puede dar una solución de mediano plazo para la toma de decisiones.
Autor: Aldo Surós Campos, Ingeniero en Producción Industrial
Bibliografía:
Domínguez, J. (1995) “Dirección de Operaciones”. Editorial McGraw-Hill, México.